Geoff Clarkson, P.Eng., doesn’t fabricate composite storage tanks, but he knows a lot about what makes them last – and fail. Clarkson founded UTComp in 2008 to offer engineering and inspection services to the composites industry. Using the company’s UltraAnalytix™ non-destructive inspection system, he has assessed dozens of FRP tanks through the years. The outlook for most of these composite assets, he says, is extremely positive.
“Composite materials seem to significantly outlast predictions by the designers, manufacturers and constituent material suppliers,” says Clarkson. “That’s a really good result.” Consider the oldest tank that UTComp has inspected – a 62-year-old tank that stores a sulfuric acid solution in a metal processing plant in Quebec, Canada. The plant owner knew the tank wasn’t leaking, but was unsure if any other deterioration had occurred. So he called in UTComp for an ultrasound analysis, which revealed the tank “is still doing extremely well in a very corrosive environment,” says Clarkson. Frp Vessel
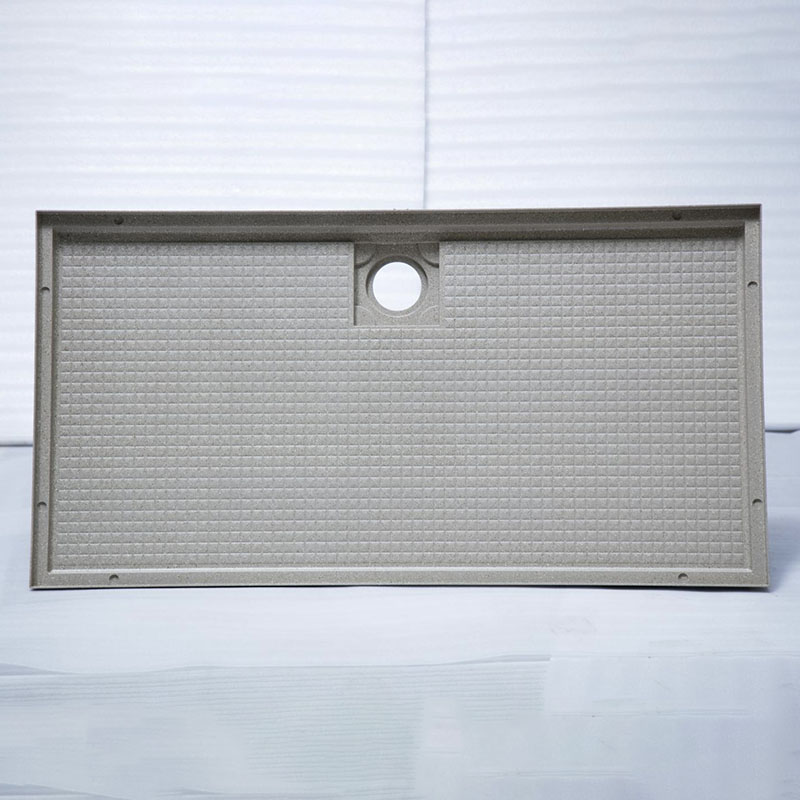
The composites industry has changed dramatically since that tank was built and installed in the late 1950s. There have been tremendous advancements in materials and technology, in addition to rising customer expectations and the adoption of numerous standards and regulations surrounding the use of FRP in storage tanks. But the longevity of composites remains one of its strongest selling points.
“FRP is designed to stay in its original watertight, functional design from the day the tanks are delivered until the end of their service life, which in most cases is the life of the building or installation,” says Bruce Coe, regional sales manager for water applications in Canada and the U.S. for ZCL | Xerxes, a product line of storage tanks within the Composite Product Systems division of Shawcor Ltd. “That’s the value proposition of FRP products. It’s not the cost today: It’s the value proposition of a composite-built tank over the next 30 to 50 years.”
Factors that Influence Material Choice
While the long life of composites is appealing, it’s not the only decision-making factor that end users consider today when selecting tank materials. “The structure, the use and the budget dictate what the customer chooses,” says Coe. In the water and wastewater market he serves, most tanks are built from concrete, GFRP and high density polyethylene. HDPE is cheaper than GFRP, but doesn’t last as long.
“The above-ground tank market changed 20 years ago with the advancement of HDPE technology,” says Coe. “As the material became better and stronger, a segment of the market made an economic decision to buy a cheaper product that may need to be replaced in 10 or 12 years instead of a fiberglass tank.” For applications where the tank is small and easily accessible, some customers are willing to foot the replacement costs because an HDPE tank may be one-quarter to one-third the cost of a GFRP tank.
However, HDPE probably won’t meet the structural requirements for tanks with about a 15,000-gallon capacity or above, says Coe. He recently got a call from a potential customer in need of six 50,000-gallon underground tanks. “That eliminates HDPE and makes FRP competitive with concrete,” he says. “It’s right in our wheelhouse to deliver that much storage to a site that’s watertight and will last a lifetime.”
Another option in the tank industry is dual laminate FRP composites, which combine a thermoplastic inner liner with a GFRP exterior. Dual laminates grew in popularity as customers required tanks that could store high-temperature gases or liquids that were more caustic or under higher pressures.
“Thermoplastic liners typically have the ability to contain all that, but don’t have the structure to support it like a fiberglass piece of equipment can,” says Tim Schoessel, president and owner of Tri-Clor Inc., a fabricator in Hastings, Mich. “In dual laminates, the two materials are married and work well together.” In corrosive environments, such as the chemical processing industry, they compete well against metals like high nickel alloys and titanium.
Increasing end user demands drive innovation in composites. “Our customers in the chemical world are trying to stretch the limits of their equipment,” says Schoessel. “If they push the boundaries, then we follow closely behind and develop the equipment they require.”
Suppliers aid the cause with new resin and fiber technology. “Materials have advanced,” says Joe Puthoff, president of Plas-Tanks Industries Inc., an FRP vessel manufacturer in Hamilton, Ohio. “We’re still using resin and glass to build the tanks, but new technologies allow us to offer better corrosion resistance [to customers] and improve efficiencies in our facility.”
The latter – improved efficiencies – is critical to fabricators seeking a competitive edge. INEOS Composites in Dublin, Ohio, is one of several resin suppliers introducing new, more efficient products to the market. In 2018, INEOS rolled out its Derakane™ Signia™ line of epoxy vinyl ester resins, which are formulated to offer faster laminate consolidation, lower foaming and reduced sanding for application of secondary laminations, according to Kevin Lambrych, manager of the INEOS Corrosion Science Center.
The Derakane Signia resins also provide improved cure kinetics. “That allows fabricators to process thicker parts,” says Lambrych. “The parts cure without excessive heat, so they don’t warp, twist or burn.” In addition, the new resins contain a novel vapor suppressant technology that forms an air activated film, thereby reducing styrene emissions during curing. “That’s beneficial to us in the plant and from an environmental standpoint,” says Puthoff.
Advancements in resins from INEOS and other leading material suppliers build upon tried-and-true technology that make composites an attractive option for tanks in a variety of industries, from chemical processing and mining to wastewater treatment and pulp and paper. Composites are corrosion resistant, strong, lightweight and flexible – all of the attributes required by a nuclear power plant in the northeast that reached out to Plas-Tanks for three storage tanks.
The nuclear power plant needed three 10,000-gallon tanks to store chemicals in its current facility. “Part of the scope requirement for us was to build tanks that could be easily installed within this existing structure,” says Puthoff. Plas-Tanks fabricated each of the cylindrical tanks in four separate pieces – the bottom, two middle sections and the top. In early 2020, the pieces will be shipped to the nuclear power plant, where Plas-Tanks’ employees will laminate the pieces together on-site.
“There’s a lot more flexibility and options with FRP than other materials,” says Puthoff. “If you get in the field and realize there’s a problem with the structure, it’s very easy to modify on-site. You can cut another hole or put a fitting in another spot. Alloys can be welded in the field, but composites don’t require traditional welding, so there’s no worry about open flames or permits to weld.”
Regulations that Impact the Market
Perhaps one of the biggest influences on the tank market is regulations. “Regulations are becoming stronger across all of our platforms. They are the driving force for all FRP products,” says Coe. “We’re not promoting these regulations, but we’re also not pushing against them. We are simply meeting our customers’ requirements.”
Interested in using composites in infrastructure? Learn more about certifications in the following areas:
ACMA's Composites Growth Initiative (CGI) committees promote and expand the use and understanding of composite materials. Join a CGI Committee related to infrastructure:
Contact ACMA
Composites Manufacturing is the official publication of the American Composites Manufacturers Association. Published bimonthly, it offers practical assessments of the current state of the composites industry as well as thoughtful explorations of the opportunities and challenges ahead. It includes timely coverage of core market segments, materials, processes and technical education plus topics such as sustainability, plant safety, operational efficiency and research advances. Subscribe to Composites Manufacturing Magazine.
The American Composites Manufacturers Association (ACMA) is the world's largest trade group representing over 3,000 companies in the composites industry in North America alone. ACMA is recognized as the premier provider of composites industry educational resources through its CAMX show, conferences, and Certified Composites Technician (CCT®) program. It serves its members and the industry by providing strong, proactive leadership in growing the composites market and technical, legislative and regulatory affairs.
American Composites Manufacturers Association 2000 N. 15th Street, Ste. 250, Arlington, VA 22201 Ph | 703.525.0511 Fx | 703.525.0743 | www.acmanet.org
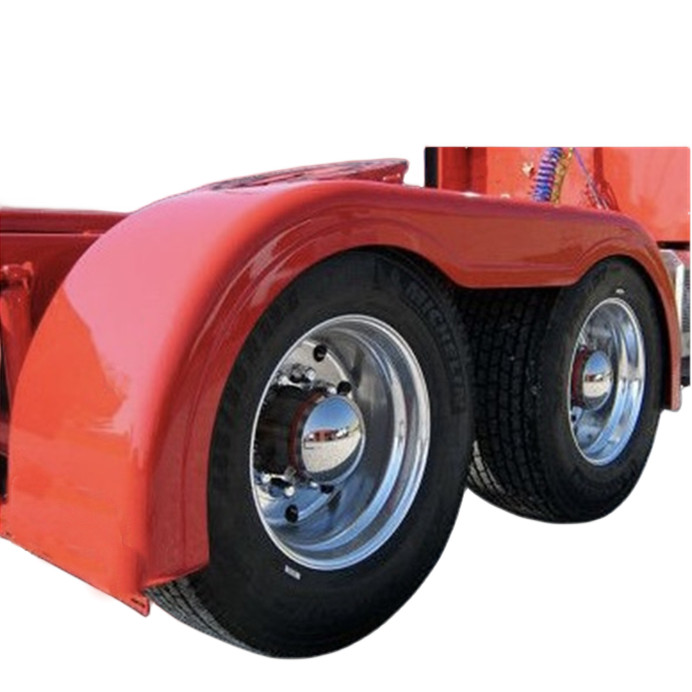
Frp Threaded Rod Copyright © 2022 ACMA. All Rights Reserved.