Recent innovations in the spinning sector focus on automation and process integration, higher efficiencies and better controls with remote access.
By Dr. Helmut H. Hergeth POY Texturing
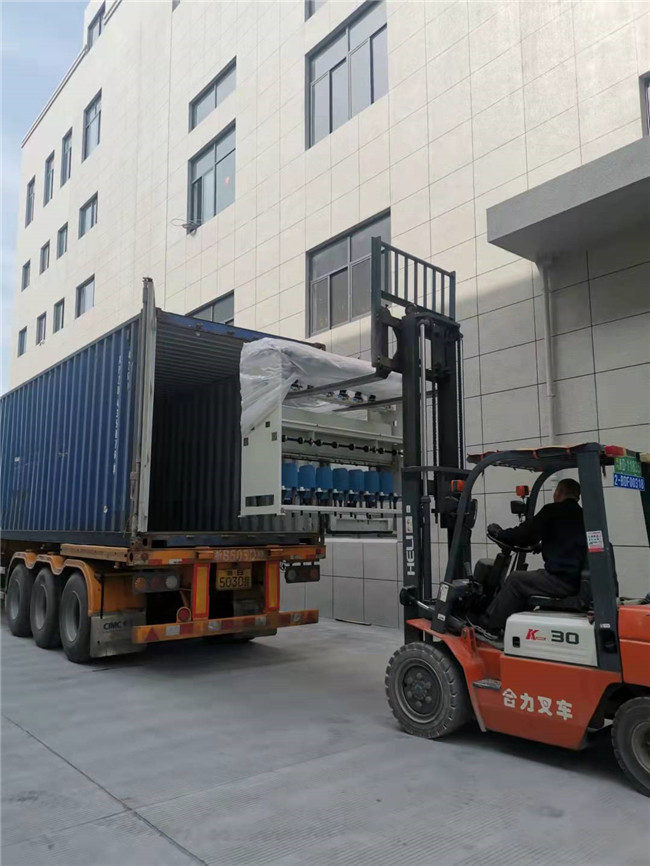
“C autiously moving forward” appears to be the overarching motto of the spinning sector at ITMA 2023 held recently in Milan, Italy. Of course there were some technical advances on display, but economically speaking, no new innovations that completely shake up existing business models. Some of the incremental investments1 of the 1980s are coming back to mind. Incremental investments allow textile manufacturers to utilize new or improved technologies without having to completely replace existing equipment. This conserves financial resources, which is relevant in uncertain economic times, as well as during times when technological directions are not yet clear. The theme of economic uncertainty was definitely visible and frequently mentioned in many conversations during ITMA.
Many machine manufacturers as well as their clients still mentioned “surviving COVID” in the post-COVID times. Economic activity is still reduced, and survival is simply more important than innovation, or at least more imminent. For equipment producers, just like for their clients, raw material prices have been very volatile and considerably higher than five years ago2. These kinds of cost increases impact machine prices, thus changing the cost/benefit analysis for new equipment and new technologies. Similar price increases and volatilities have taken place in raw materials for yarn producers — in cotton and polyester2 prices, for example — making long-term decisions like the purchase of new spinning equipment extremely difficult.
Additionally, like for most other industries, a lot of technological innovation is happening in the integration, control and coordination of textile processes. This upgrade requires computing equipment and semiconductors — items that are still in supply chain recovery mode since 2018. Shortages in some cases lead to “allocation” of equipment to existing or strategic customers only, most definitely not a desirable situation for the industry. Some themes do emerge in the technology directions despite this economic backdrop.
Most of the equipment manufacturers at ITMA showed very sophisticated programs that monitor, control, optimize, and integrate processes within and between plants. Cloud computing, remote access and control, and a plethora of data analyses was shown by most of the companies at ITMA. Software programs are key to efficient plant management, and exhibitors integrate maintenance and spare part businesses into their plant management toolboxes. While spare parts have always been an important business component, today these services are strongly promoted, showing how much more important they have become to the suppliers.
MyTrützschler — available from Germany-based Trützschler Group SE — for example, allows users to access to detailed plant information with live feeds from practically any-where. The MyWires functions help optimize card clothing management, whether the spinning mill conducts its own wire maintenance or utilizes the service provided by Trützschler. Technologically, this kind of real time data allows for optimized plant management, optimized equipment maintenance, and faster and better decision making. Economically, it also shows how much more integrated the supply chain on the textile equipment side is. Not only are the textile equipment manufacturers much more integrated in bale handling through spinning, but also any of the auxiliary suppliers— such as monitoring and maintenance, for example — are tied into the supply chain through acquisitions and strategic alliances.
In similar fashion, digital solutions offered by Italy-based Marzoli Machines Textile S.r.l. optimize the spinning process and monitor key performance indicators (KPIs) in real time. According to the company, implementing its predictive maintenance program analyses a large volume of company data against benchmark values, resulting in maintenance cost savings of up to 30 per-cent. Using the cloud based marketing resource management (MRM) soft-ware, problems can be analyzed remotely and energy consumption and efficiencies can be optimized.
On the equipment side, Trützschler showed the TC 19i card at ITMA 2023, with the T-GO gap optimizer, which automatically fine-tunes the carding gap to compensate for changing temperatures and conditions during operation, leading to higher production and better quality. The optical sensor of WASTECONTROL continuously monitors the waste quality at the licker-in and automatically optimizes the mote knife setting via the servo motor. With rising raw material costs, any raw material savings are an important cost factor, no matter what textile market is served. NEPCONTROL data is monitored and uploaded to the MyMill system, where any deviation in nep count can be analyzed and addressed at the machine level from anywhere in the world. The TC 30i card has been updated since Barcelona and shows an increased carding area — with approximately 1/3 more active flats plus a precarding and post-carding zone. While an increased carding surface is not a new idea or technology, the existing carding technology has certainly been improved, leading to higher production levels, better quality and more efficient waste management —including minimizing fiber waste and separating waste fibers to optimize the recovered value. Similar improvements can be seen in drafting — like the self-optimization of Trützschler’s TD 10 — leading to higher efficiencies, improved quality monitoring and better integration of mill management.
Switzerland-based Rieter showed very similar directions in its developments, with the C77 and C81 carding machines featuring an increased carding surface — the company reports the C81 sports the “largest active carding area” in the market — automatic Carding Gap Control and optimized fiber yield using its Trash Level Monitor. Improvements in its spinning machines also continue, for example in ring-spinning with the G38 and G37 models; rotor-spinning, like the fully automatic R70; or in compact spinning, like the K48. How-ever, the J70 for air-jet spinning was specifically highlighted at ITMA. With a roughly 25-percent higher production speed compared to ring spinning and unusually high flexibility offered via the VARIOlot option — up to two different lots per machine side — the J70 matches the ever-changing market demands for smaller lot sizes. Cost and flexibility remain relevant.
Marzoli showed the FTM320 roving frame with the central headstock in the middle of the machine. This layout not only simplifies managing the machine itself and optimizes automated transport of bobbins to the spinning machines, but it significantly reduces exchange and cleaning times by almost 30 percent, according to the company, thus increasing efficiency and reducing cost — specifically energy cost — which is of course an ongoing concern in the textile industry. The layout of the FTM320 also reduces space requirements, and while looking at productive area versus non-productive area is not always one of the most urgent decision criteria considered, in some cases, space becomes an absolute deal-breaker or deal-maker. Marzoli’s MDS2 spinning frame also offers improved efficiency and reduced energy consumption, inline with the concerns of the industry. Energy consumption, and specifically air consumption, also are the key improvements seen in Marzoli’s comber CMX, with increased productivity and up to 10 combing heads.
In addition to the high degree of automation within each of the machines, from self-correcting adjustments to automated and integrated maintenance, Marzoli also showed the integration between machines. Automated transport and coordination between combing, roving, and spinning are key elements in addressing concerns about labor availability and reliability.
An overarching theme for Rieter also was automation and integration. Its ROBOspin fully automated piecing robot now is also available for compact spinning machines. Improved control systems allow quality control going into and out of the machines, and Rieter helps mills with its Rieter Digital Spinning Suite to monitor, manage and optimize spinning mills remotely. Service, maintenance, and spare parts, as well as carding wire management are an essential part of the Rieter business model.
Saurer Intelligent Technology AG, Switzerland, also showed automation and process integration as a major theme. Like most equipment producers, it addresses automation as a managerial response to rising labor costs worldwide and independent of cost automation, which helps address reduced avail-ability of skilled labor in the industry. All equipment manufacturers mentioned training programs at ITMA —in person, online, or at the machines — as well as automation in order to address various labor issues — skill levels and ongoing training, availability and cost — that are an industry concern worldwide. Saurer offers training through the Saurer Academy. Additionally, automation and process integration can improve quality and efficiency by reducing human error. Saurer specifically showed the Autocard SC7 carding machine— which features automatic gap adjustment for recycling, and increased carding surface area for improved quality and production rates — and automation in automatic transportation or “linking” from one process to the next.
The ZI 72XL compact spinner, the Autoairo air spinning machine, the Autocoro 11 and BD8 with Twinsuction on both ends rotor spinning machines, and ZI 451 worsted com-pact-spinning machine were on dis-play, as well as twisters, cablers, and winders. Energy efficiency and reduction of energy consumption are an important topic in spinning, where energy cost often exceeds the cost of direct labor. Saurer addresses this through its Texparts product line, which introduced a smaller diameter spindle, Eshape, to reduce energy costs, among other variables.
Automation in process and product monitoring and inspection is of course a key component in any textile manufacturing setting, and Switzerland-based Uster Technologies AG showed the 360Q solution suite as a fully integrated system helping with data generation, analysis, and solutions for quality as well as cost management. This leader in textile testing and monitoring has integrated in-line monitoring at all levels with analysis and decision-making tools. Human error is essentially removed from the equation. The RSO3D, Uster Quantum, and Uster Sentinel are key elements in mill management that existing and new spinning mills need to remain competitive.
The Yarn Master PRISMA from Loepfe Brothers Ltd., Switzerland, offers superior clearing with its dual measurement system — infrared and mass sensors — thus improving quality while saving costs — two key business drivers in yarn production. Using an innovative Autostart feature, set-up times are drastically reduced, allowing for faster and less costly product changes, which is a key aspect of agile manufacturing. Integrating software enables a complete management system, and as additions to existing equipment Uster and Loepfe technologies have always been part of new and incremental investment strategies in the industry.
Italy-based Savio Macchine Tessili S.p.A. also showed trends towards more automation with its Proxima Smartconer automatic winder, for example; and increased flexibility in air-jet spinning with its Lybra Smart-spinner, which allows changing fiber blend ratios in the yarn from two slivers via computer (See “Just A Few Of The “Cool” Things On Display — The ITMA 2023 Edition,” TW, July/August 2023).
There was much anticipation surrounding Japan-based Toyota Industries Corp.’s Helix vortex spinning machine, but unfortunately the machine was not on display at ITMA. Only videos were available to customers. According to company associates, production speeds are in the 50,000 revolutions per minute range with very fast start-up speeds. This technology is something to look forward to seeing in person at ITMA 2027!
Murata Machinery Ltd. (Muratec), Japan, manufacturer of the Vortex spinning system, had only a small booth with videos and chose not to display any machines at ITMA. France-based NSC/N. Schlumberger SAS showed similar directions of improvement — in automation, energy savings and process integration— for long-staple-fiber yarns.
Spain-based Spinhole® Consulting offers consultancy services to help spinning mills change the configuration of the drafting zone and yarn guides to create a double “multi” balloon, allowing increased production speeds, reduced energy consumption, and thus reduced costs— a true incremental investment as defined above.
Italy-based C.P.S.TEX S.r.l. with its Greenspin technology, offers similar retrofitting drafting systems for worsted and woolen ring spinning machines.
Also, in winding, companies such as Dietze+Schell Maschinenfabrik GmbH & Co. KG and Georg Sahm GmbH & Co. KG, both based in Germany illustrated the trend towards more automation, higher production, increased flexibility — like the Flexible Traverse option from Sahm — as well as remote support and service.
It should be noted that in addition to the traditional spinning machinery producers, there are equipment producers from India — Lakshmi Machine Works Ltd. (LMW®) for example — or China — such as Jingwei Textile Machinery Co. Ltd. — that offer a full range of equipment for spinning mills.
All major manufacturers of spinning equipment showed not only how energy consumption has been reduced, but also how the technologies can contribute to a circular economy. Recycling has moved from an also mentioned ability to a separate business concept that warrants complete business segments within the companies with dedicated equipment from opening through spinning. At ITMA, manufacturers market dedicated product lines specifically for recycled materials — such as TRUECYCLED by Trützschler or the COM4 Recycling process by Rieter, for example — and with raw materials being the biggest cost factor in textile processing, recycling makes sense economically as well as environmentally. Being able to process obsolete products into raw materials is as essential in the circular economy as any other step within this circle.
All of the equipment manufacturers also describe reduced energy consumption in their products; this is of course an ongoing trend, and economically highly relevant as energy costs in spinning tend to be more relevant than labor costs. Managerially speaking, cost savings are always easy to justify, especially when these costs are getting more volatile. Additionally, reduced energy consumption results in a smaller carbon dioxide footprint, which is good for the environment and a company’s corporate social responsibility report. While these are all easy concepts to sell, they are not necessarily easy concepts to implement into the equipment, and tend to make equipment more complex and difficult to maintain. This is where remote training programs, and service and maintenance programs offered by the manufacturers become an integral part of the business models.
The world economy is still recovering, and supply chain issues — specifically in the electronics areas — impact spinning equipment like any other machinery. In terms of innovation, there is not a completely new mouse-trap, but the existing mousetraps are continuously improving — higher efficiencies, more automation and process integration, better controls, and remote access. Most equipment features self-correcting systems that ensure higher speeds, more flexibility, and better quality. Simultaneously, manufacturers are aligning with cultural trends toward sustainability by embracing energy efficiency and product lines for the circular economy.
1. H. Hergeth, “Investment strategies for stagnating industries”, in the series Empirical Economic Research Vol. 1, Münster, 1986. Also, H. Hergeth, Incremental Investments and their Results in the Textile and Apparel Industries, Ars Textrina 26, 1996, pp. 65-79.2. Federal Reserve Bank of St. Louis, Commodity Prices for various products, https://fred.stlouisfed.org/.
Editor’s Note: Dr. Helmut H. Hergeth is an associate professor in the Wilson College of Textiles at North Carolina State University, Raleigh, N.C.
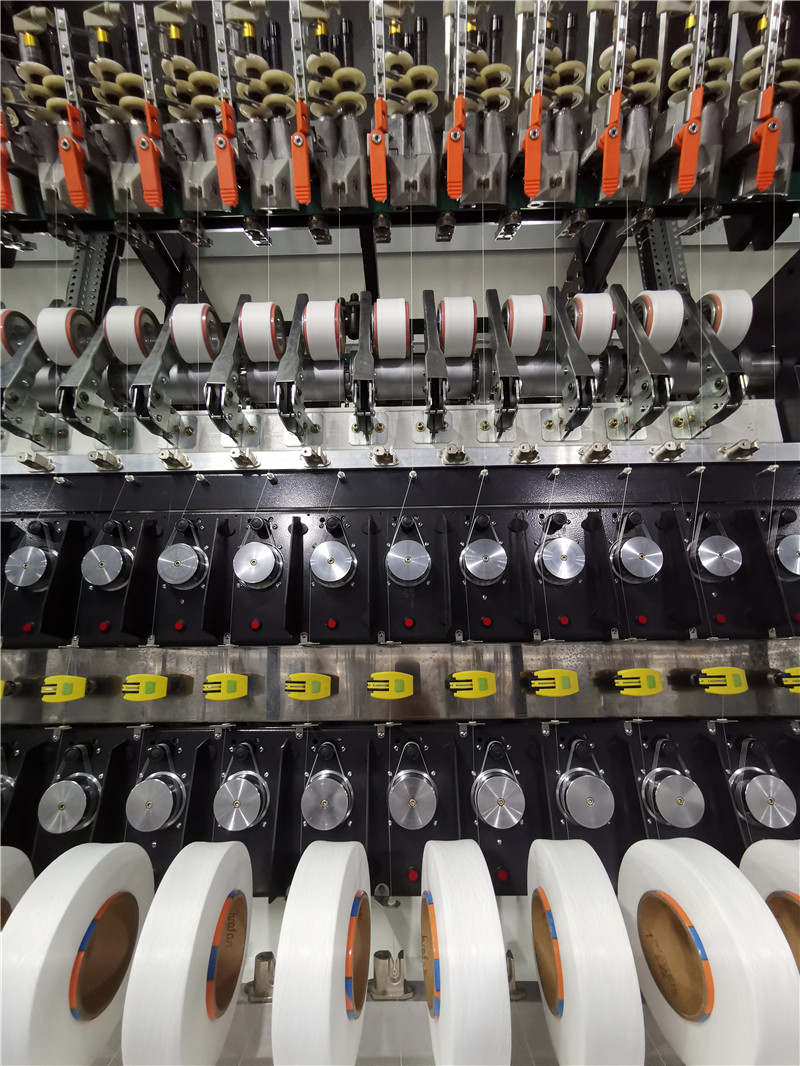
Fancy Yarn For Knitting View Latest Digital Issue »