Editor's note: This story first appeared in the January-February 2023 issue of Offshore magazine. Click here to view the full issue.
By Jeremy Beckman, Editor, Europe Water Cool Air Dryer
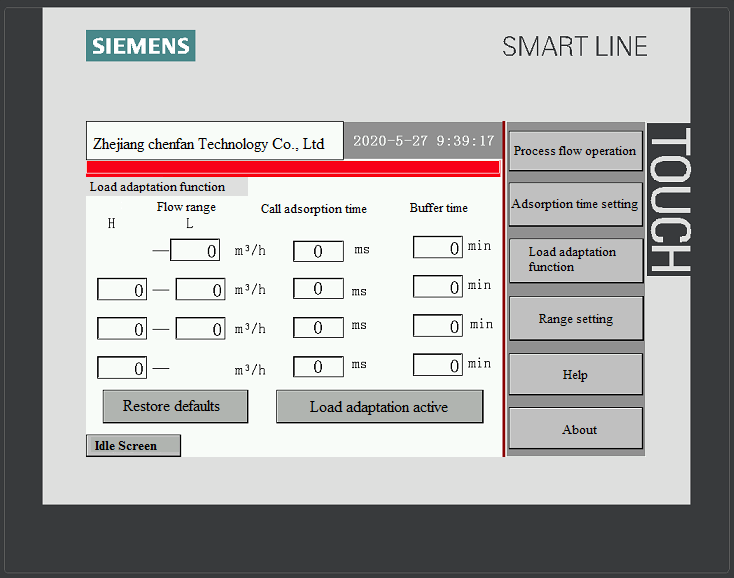
Trials will start shortly on a full-scale prototype of Worley’s pseudo subsea dry gas/liquids separation technology. The six-week program at the TÜV SÜD National Engineering Laboratory (NEL) in Glasgow, Scotland will involve tests at different pressures of various combinations of hydrocarbon fluids, water and simulated production water. A successful outcome would bring the development closer to the full technical readiness level needed for a first offshore field trial.
Worley’s Intecsea consultancy initially devised the concept in 2017 as an alternative to transporting multiphase fluids (gas, condensate and water) via long-distance subsea tiebacks of 100 km or more. The Pseudo Dry Gas (PDG) process employs in-line piggable separators to remove liquids (condensate and water) in the main gas pipeline system at volumes of up to 100 bbl/MMcf. The liquids are then held in drop-out vessels, one located on each side of the main pipeline, for a residence time of around 10 minutes to ensure satisfactory final separation before being transferred via subsea pumps to a smaller-diameter liquid line running alongside the gas pipeline. At the same time, the liquids-stripped (dry) gas continues traveling through the main pipeline to the host process plant. The technique is said to eliminate gravitational pressure losses in the system.
The stand-out benefits, according to Worley, are the potential to substantially extend subsea tiebacks out to 200 km or more, and to increase recoverable gas volumes through lessening backpressure on the reservoir; substantially lower development capex than standard solutions such as FLNG vessels, subsea compression, or floating/fixed facilities that process the fluids before sending them to shore; and a much lower power requirement for the PDG’s separation method compared with topsides or subsea compression, which in turn greatly reduces the carbon (scope 1 and 2) intensity per unit of produced hydrocarbon. And by accommodating a greater degree of liquid uncertainty, the concept theoretically reduces production risks, while the lower back-out pressure allows for increased phasing of wells without loss of reserves.
During 2017, Worley secured the first funding for engineering definition and computational flow dynamics (CFD) studies before embarking the following year on engineering definition of all the related hardware, the power system and the liquid removal process. The team, led by Lee Thomas, the concept’s co-inventor, also performed a study with the Net Zero Technology Centre in Aberdeen of four development scenarios for a 195-km tieback of multiple (real) stranded gas fields west of Shetland in 1,700 m water depth. This assumed a design flow rate of 500 MMcf/d from eight wells with initial reservoir pressure of 345 barg, a liquid-gas ratio of 6 bbl/MMcf, and in-place gas resources of 2.8 tcf.
The four arrangements studied were a gas FPSO export pipeline for the gas to the shore; a dual-flowline (2 x 18-in.) tieback to a new onshore plant with deferred onshore compression; a similar dual-flowline tieback to a new onshore plant but with deferred subsea compression; and a Pseudo dry gas tieback to a new onshore plant with deferred onshore compression. As reported in an OTC paper, the variable power demands were derived from integrated production modeling linked to flow assurance models, which showed the reduction of well pressure as a function of time and production for each of the four concepts. Pipeline diameters and design pressures were calculated based on analyses using steady state and transient flow assurance simulation software, with monoethylene glycol (MEG) included, to determine appropriate functional operating envelopes such as turndown, backpressures and liquid surges.
Among the chief findings concerning the pseudo dry gas option were a 67% reduction in energy intensity, without impact on production. This was due to the concept’s focus on changing the nature and shape of the resistance curve within the tieback over the operational envelope, which maximized the use of the reservoir’s existing energy. Both pseudo and subsea compression also led to enhanced economic outcomes, while pseudo emerged as competitive against the dual-flowline options as the extra costs incurred offshore were offset by reduced equipment requirements onshore (i.e. no need for a slugcatcher). The overall cost for the PDG option was projected at $3.3 billion (from drilling to the new onshore plant), with anticipated revenues of close to $10 billion over field life, making it the most attractive of the four concepts. Upstream CO2 emissions were also 65-80% lower than the other studied concepts, in large part due to the elimination of compression.
With further support from the NZTC and industry funding, Intecsea then started work on a 6-in. scaled prototype of the liquid-removal unit with Strathclyde University in Glasgow, a 12-month design process. Input for the CFD models was derived from flow assurance models from previous field development studies. The prototype, housed within a clear acrylic material, was designed as a construction set with interchangeable parts to enable 11 different configurations for the 7-bar hydrotesting program that followed at Cranfield University’s flow loop north of London in 2020. The fluid used for these experiments was an air and water mixture at atmospheric pressure. Parameters tested included uphill and downhill inclinations of the prototype; varying levels in the drop-out vessels (10-70%); sand testing at 1% volume in water; smaller-diameter, shorter-length gas return pipe; base case with larger cans and with different internals; and with an inlet spool to the gas-liquid separation chamber at 11° inclination and 22° inclination, at O° and 2° inclination uphill.
None of the configurations tested exhibited a detrimental impact on the liquid removal efficiency compared to the base case. Sand was shown to accumulate in the drop-out vessels, but this did not degrade the performance of the PDG module. And installation roll was shown to have no impact on the operation of the module, due to its robust design. Overall, the results were in line with the anticipated operating envelopes for long distance gas/gas-condensate tiebacks. This, along with the supporting CFD to address inconsistent parameters from the scaling analysis, appeared to justify the next phase of testing at higher pressures of a carbon-steel PDG prototype.
For the next phase of pre-production tests at NEL, Worley has secured $1.2 million in funding from Scottish Enterprise for fabricating a large-scale PDG unit and procuring a magnetic drive subsea pump and a supporting subsea control system, operating at pressures of more than 130 bar, with a variety of hydrocarbons. The aim is to extend the development’s current technology readiness level from TRL4 to TRL5: at that point, according to Thomas, a pilot offshore project could be viable following enhanced factory acceptance testing of a full PDG equipment set-up integrated into a pipeline system. “An ideal pilot would be maintaining gas production from an existing tieback post-water breakthrough in an MEG-constrained environment," Thomas said.
“The dimension of the structure being tested at NEL is 10 x 2.5 x 2.5 m,” he continued, “related to the 180-bar design pressure and a weight of 16 metric tons. While Worley designed the overall functional system, the company used high-quality suppliers to undertake the detail design of key components aligned to the functional requirements. The subsea pump with magnetic drive coupling, supplied by FSubsea in Oslo, weighs about 1.2 metric tons and has undergone successful post-Factory Acceptance Testing. It has a design rating of 150 bar, and a duty point of 10 bar and 15cu m/hr. Furthermore, a recycle loop has been included within the wider pump skid so that for low liquid flowrates the output from the pump can be below its minimum stable flowrate. This is important as it is a requirement often seen in field study cases for the PDG.
“We have rented a subsea control system from Proserv in the UK, based on a 15-year old subsea control module which was manufactured as an operational spare but never deployed. Lavar Shipping in Cyprus is fabricating the PDG structure and pump piping skid, and is also conducting some development testing related to pre-commissioning of the system. Worley and Proserv have written the software application to fully automate the pump with inputs from the instrumentation, as expected in a full operational system.”
Two different hydrocarbons will be tested, a very light oil and a light condensate. Surfactants have been added to lower surface tension as nitrogen is being used for the gas, since this better represents the expected conditions near the wellheads. “Additional fluids to be tested are simulated production water to represent biogenic gas fields and a mix of water and hydrocarbon. All testing will be at 0° and 2° inclinations to represent that the subsea is rarely flat.”
Flow behavior specialists at the University of Western Australia School of Engineering are providing simulation support, using the school’s laboratory and pilot-scale experimental facilities. “UWA are involved in creating an ‘App’ extension program for OLGA simulation software that will take the results from the testing and enable PDG to be designed for dynamic conditions with OLGA.”
Theoretically, Thomas said, the technology could be adapted for long-distance tiebacks to (part-electrified) floating or fixed gas platforms – currently not feasible – without the need for major topside modifications. “This is one of the technology’s strongest points as the power design is normally less than 0.5 MW and a slug catcher is not required. In our study work we have also found that by lowering the flowing pressure in the pipeline and removing the fluids from the gas, corrosion rates are reduced by >50%. This means a PDG system could handle gas reservoirs with greater associated contaminants than a normal carbon steel tieback could. Worley has also refined the design process so that typically for a tieback of 200 km or more, only one unit would be required, located within 30 km of the gas field.”
Thomas further noted that the PDG system is designed for the full life of field, and the system is piggable. This means that “the pipeline can be inspected as per industry norms. The PDG unit itself has no moving parts hence very little to fail. Components which can fail are 100% redundant, such as pumps, power systems and instruments. Furthermore, all components that could fail have the ability to be retrievable via vessel intervention. Another strong point is that no component to date from design work weighs more than 50 metric tons, so any maintenance work can be done with a standard support vessel, with no requirement for heavier construction vessels for intervention.”
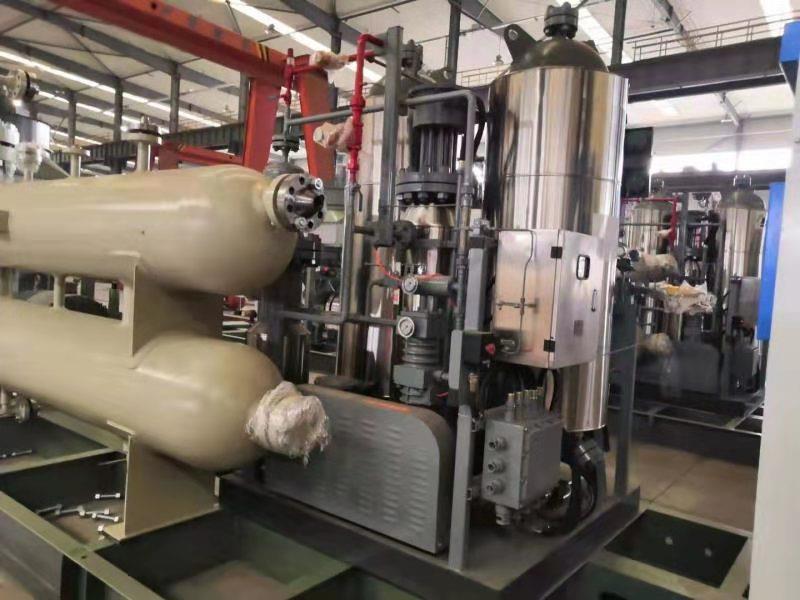
Water Cool Air Dryer Another potential application is stranded gas for conversion to blue hydrogen onshore. “Many parties within funding and governmental organizations have identified insufficient development of technology to really lower the scope 1 and 2 emissions from gas fields that will be needed as the feedstock for blue hydrogen, hence PDG can been seem as a natural partner for blue hydrogen as the lowest emissions feed stock. We have seen multiple studies where we lower scope 1 and 2 emissions in excess of 90% due to the removal for the need of compression, be it topside or subsea.”